The bug Mario refers to would only affect you if you used clock_idle=true. This is because the SPI firmware always sets clock to false after the transaction.
The bug has no effect if using clock_idle=false.
The WS2801 spec says it's good for up to 25MHz clock speed. Don't try to set 25MHz though because you will end up with 48MHz. You should be able to use 24MHz though if you keep lead length short. But there's no reason that 2MHz shouldn't work.
You could try running the strip at Vcc=4V or less. Add a couple of 1N4007 diodes in series to drop the voltage. The chip is spec'd for 3.3-5V VCC but obviously the LED intensity would be lower. This would only be to prove that the logic hi level is not the issue.
For those reading this thread who haven't looked at the data sheet the specification for a logical high input level is 0.8* Vcc. With Vcc at 5v this means a minimum voltage of 4v is required to be certain it is registered as logic hi. Netduino can only put out 3.3v on the outputs.
Since your chip does not use the CS, you should use CS = GPIO_None. Pin 13 on the mini is the only pin that you can't use for CS (with the currently released firmware) the same is true for Pin 4 on the netduino(&plus)
This is due to some functionality in the .NETMF porting kit that was abandoned but not completely removed.
I can't see how this could stop your code from working though.
Are you using the latest firmware? 4.1.0.6 or 4.2?
If I were you, I would buy myself an Open bench logic sniffer from Seeed studios. It'll be the best $50 you've ever spent.
A logic shrimp or a bus pirate might even be sufficient. Or borrow an oscilloscope from someone.
I duplicated Stefan W's sample on my Netduino plus (FW4.1.0.6) and got a different result.
Here is my sample taken using the Logic Sniffer
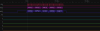
public static void Main() { byte[] buffer = new byte[] { 0x55, 0xFF, 0X00, 0X55, 0XAA }; SPI.Configuration xSPIConfig; SPI xspi; xSPIConfig = new SPI.Configuration(Pins.GPIO_NONE, false, 0, 0, false, true, 100, SPI.SPI_module.SPI1); xspi = new SPI(xSPIConfig); while (true) { xspi.Write(buffer); Thread.Sleep(100); } }
Even at 100kHz there is nothing like a 500us break in the transmission. The GC (garbage collector) may run between bytes during an SPI write comman making a slightly longer delay between bytes but it would never get to anything like 500us.